Pressure Gauge
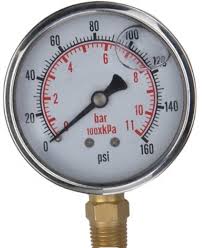
Pressure Gauge
A Pressure Gauge is a crucial instrument used to accurately measure the pressure of gases or liquids in a closed system. It provides vital information about the system’s operational status, ensuring safety and efficiency in various industrial processes and applications.
Design and Functionality: Pressure gauges typically feature a circular dial displaying pressure readings in units such as psi (pounds per square inch), bar, or kPa (kilopascals). The dial is usually marked with a pointer indicating the pressure level. The gauge’s internal mechanism, often a Bourdon tube, diaphragm, or bellows, reacts to pressure changes, translating them into mechanical motion that moves the pointer across the dial.
Types: Pressure gauges come in various types, including analog (mechanical) gauges and digital gauges. Analog gauges rely on mechanical components for pressure measurement, while digital gauges use electronic sensors and displays to provide precise readings. Additionally, pressure gauges may be classified based on their application-specific features, such as low-pressure gauges, high-pressure gauges, differential pressure gauges, and vacuum gauges.
Construction Materials: Pressure gauges are constructed from durable materials such as stainless steel, brass, or aluminum to withstand the conditions of different environments. The choice of materials depends on factors like the type of fluid or gas being measured, temperature, pressure range, and corrosion resistance requirements.
Pressure Range: Pressure gauges are available in a wide range of pressure ratings to suit various applications. These may include low-pressure gauges for delicate measurements and high-pressure gauges for demanding industrial processes. The pressure range is typically specified in the gauge’s technical specifications and may vary from vacuum to thousands of psi or bar.
Applications: Pressure gauges find applications across numerous industries, including manufacturing, automotive, oil and gas, petrochemical, pharmaceuticals, HVAC (heating, ventilation, and air conditioning), water treatment, aerospace, and marine. They are used for monitoring and controlling pressure in hydraulic systems, pneumatic systems, pipelines, storage tanks, boilers, compressors, and many other industrial processes.
Features: Modern pressure gauges often come with additional features such as liquid-filled dials to dampen needle vibrations, over-pressure protection to prevent damage from pressure spikes, and corrosion-resistant coatings for extended durability in harsh environments. Digital pressure gauges may offer advanced functionalities like data logging, wireless connectivity, and customizable display options.
Installation and Maintenance: Proper installation and regular calibration are essential for ensuring the accuracy and reliability of pressure gauge readings. Maintenance tasks may include checking for leaks, verifying calibration, and replacing worn-out components as needed.